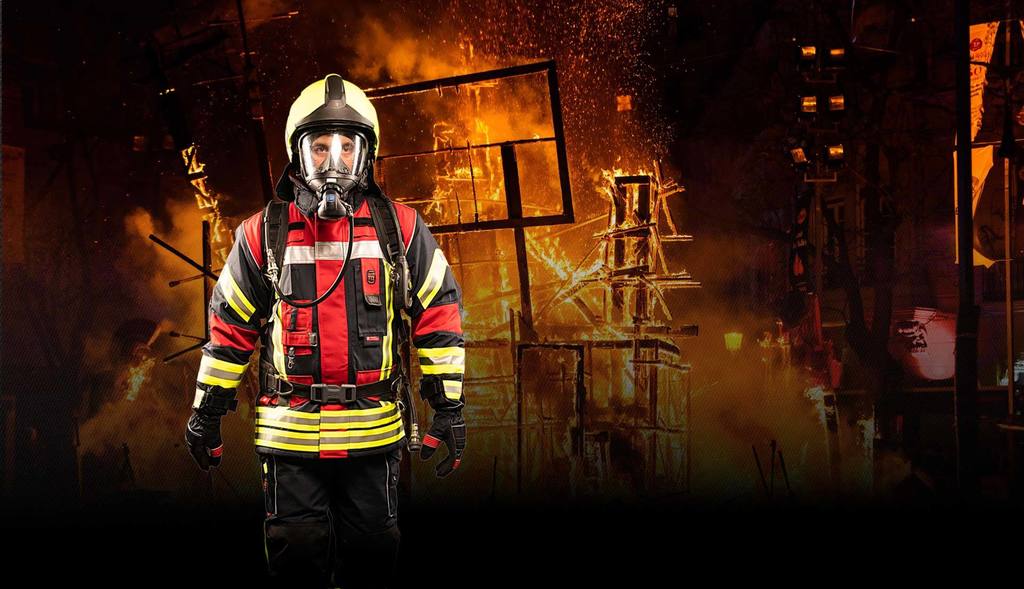)
Fire brigade protective clothing
Standards, regulations, guidelines and recommendations
What is BS EN 469 and what changes has the new BS EN 469:2020 brought?
The basic standard for protective clothing, BS EN 469, is entitled "Protective clothing for firefighters – Performance requirements for protective clothing for firefighting activities". As a harmonised standard, the standard is valid in the member states of the European Union and some other members of the "European Committee for Standardisation" CEN, such as Norway, Switzerland, Turkey among others.
It is used in the individual countries as a national standard with the same content, e.g. in Germany as DIN EN 469, in Austria as OENORM EN 469 or in Sweden as SN EN 469.
The standard, which was published anew in 2020, has some minor changes: Testing the heat transfer between flame and radiation is performed both in a washed and unwashed state; the testing of contact heat is new; instead of the spray test, merely the penetration against liquids is tested, whereby the volume of the four test liquids (H2SO4, HCl, NaOH and o-xylene) has been reduced to two (H2SO4, o-xylene); the tear resistance was increased from ≥ 25 N to ≥ 35 N and the seam strength from ≥ 225 N to ≥ 300 N.
What do the different performance levels of fire brigade clothing mean in BS EN 469?
BS EN 469 describes the minimum requirements for firefighters' protective clothing, and is intended to provide protection against heat and flame, as well as mechanical and chemical stresses. In addition, the clothing should provide for good wearing comfort and sufficient visibility during use. The revision of BS EN 469 published in 2020 emphasises two performance levels already in its first section and by doing so gives them a higher priority than the predecessor version from 2008.
Based on a risk assessment, a distinction is made between activities with two levels of performance:
Level 1: Minimum clothing requirement for external firefighting operations and supporting activities.
Level 2: Minimum clothing requirement for fire-fighting and rescue in internal operations.
The results of the tests required for certifying the garment in an accredited testing institute are decisive for assignment to a performance level. Here, the results of the tests for "heat transfer flame" and "heat transfer radiation" (X1 or X2), membrane waterproofness (Y1 or Y2) and water vapour transmission resistance Ret (Z1 or Z2) are compared with the requirements of the standard and assigned to performance level 1 or 2. In order to reach protection level X2, the specification "Protection against contact heat" also needs to be met. The three performance levels X, Y, Z achieved need to be shown on the garment labelling pictogram.
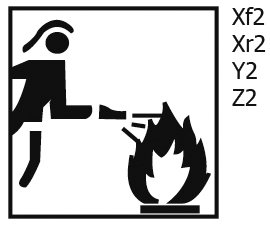
What does the HuPF describe and how does it differ from BS EN 469?
The abbreviation HuPF in German stands for "Herstellungs- und Prüfungsbeschreibung für eine universelle Feuerwehrschutzbekleidung" (Manufacturing and testing description for universal firefighter protective clothing) and is a design standard for firefighter protective clothing that is only valid in Germany. It is divided into four parts:
Part 1 Fire brigade jacket,
Part 4 Fire brigade overtrouser,
Part 2 fireman's trouser,
Part 3 fireman's jacket.
A full comparison would be too far-reaching, but one can roughly say that BS EN 469 forms the basis for the HuPF, but that the latter contains further, additional tests and is therefore more comprehensive.
In contrast to BS EN 469, the HuPF specifies a maximum garment weight, the membrane is also subjected to an abrasion test and a cold buckling test, a sprinkle test needs to be carried out and the colour fastness of the outer fabric (discolouration through washing or discolouration of accompanying fabrics, etc.) are tested. Another very important difference is what is referred to as the Thermoman Test, which is mandatory for the HuPF, whereas flaming of the entire suit is only optional in BS EN 469.
The HuPF also goes further in assessing wearing comfort. In addition to the Ret value, the what is called the Kf value (sweat transport during "liquid sweating") is also used (see the question "What is the Ret value?").
What specific recommendations are there for procuring new firefighter protective clothing?
The DGUV (German Social Accident Insurance) publications offer concrete help here, namely DGUV Information 205-014 "Selection of personal protective equipment for fire brigade operations - based on a risk assessment" and DGUV Information 205-020 "Fire brigade protective clothing - tips for procurers and users" (in German only).
In the former, the risk assessment becomes the central instrument which has to precede the procurement. The main focus is always on the part of the body to be protected, the level of protection sought and the underlying set of rules. Ultimately, a distinction is then made between internal fire-fighting, external fire-fighting, technical assistance, water rescue, rescue service and CBRN deployment.
For internal fire-fighting operations, only performance level 2 from BS EN 469, i.e. X2, Y2, Z2, comes into consideration, but with the recommendation for additional tests according to HuPF, which is considered more relevant in practice. The question of compatibility with other PPE, i.e. gloves, protective hood, helmet, footwear and breathing apparatus also represents an additional aspect.
External firefighting is combined with technical assistance, whereby one can differentiate between "waterproof" and "non-waterproof". The reference standard for "waterproof" remains BS EN 469 (with the addition of the HuPF), for "non-waterproof" the standard BS DIN EN 11612 ("Protective clothing - Clothing to protect against heat and flame") applies. Since technical assistance is generally also provided outdoors, a waivering of waterproofing and penetration with liquid chemicals is worth discussing.
Practical testing of the PPE and additional selection criteria provide a very comprehensive basis for an overall purchasing decision.
The 2nd DGUV publication dispenses with the formalism of hazard analysis, which the unsuspecting person needs to get used to, and clearly sums up the standard requirements of BS EN 469 and separates them from the HuPF.
The publication provides a number of practical recommendations for procurement and tendering.
What does the PPE regulation describe?
The new PPE Regulation (EU) 2016/425 has been in force since April 2018. The previously applicable PPE Directive (89/686/EEC) has been replaced by the new regulation.
The PPE regulation regulates the requirements and guidelines for the sale of personal protective equipment. This contains the basic safety requirements that personal protective equipment has to fulfil in order to ensure the health of the wearer and to prevent hazards.
In order to b bale to adapt the labelling, manufacturer's information and declarations of conformity for all related products accordingly, a transitional period of one year was introduced, which ended on April 20, 2019.
Products in circulation whose type certificates were issued under the PPE Directive (89/686/EEC) are not all allowed to be labelled under the new regulation after the end of the transitional period. These can even be sold until 21.04.2023, provided that a valid model test certificate is available and the expiry date has not been exceeded. From this date, only clothing that is manufactured and certified in accordance with the PPE Regulation is allowed to be placed on the market.
The main changes are as follows:
-
The period of validity of the EU model test certificates is limited to 5 years: <b } the validity of the EC-model test certificates used to be partly unlimited. However, this changes with the new PPE regulation. For this purpose, manufacturers must have their products tested every 5 years by a certification body (Cat. II and III PPE) or themselves (Cat. I) to determine whether the product meets all requirements.
-
Declaration of Conformity/Address: From now on, the manufacturer has to ensure that every product is accompanied by an up-to-date declaration of conformity and not, as was previously the case, on request. The option of making this available on the manufacturer's website is also possible. The link to this should be given in the manufacturer's information and can be accessed with just a few clicks.
-
Obligations of the economic operators <b } Furthermore, PPE Regulation Chap. II deals in detail with the obligations of economic operators, such as manufacturers, importers, distributors, etc. You can read about this in the Official Journal of the European Union.
Materials used and their treatment
Which outer fabrics are used in fire brigade protective clothing and what is the difference between Nomex, Kevlar, Kermel and PBI?
The basic requirement for the use of fabrics by fire brigades is, in general, that they are non-combustible. Both synthetic and natural fibres are used to produce the fabrics.
1. Synthetic fibres
The advantage of the synthetic fibres described below is that they are inherently non-flammable or, as they say, inherently flame retardant.
The most important materials here are:
1.1 Aramids
The name Aramide is a combination of the chemical name Ar<2 }omatic Polyamide. This means we are dealing with a chemical fibre that is formed by what is known as polymerisation. This is understood to be the chemical combination of a monomer molecule with itself or two different starting molecules to form a so-called macromolecule. This can be imagined as a line-up of molecular building blocks along a string of pearls. In the case of the aramids, two spatially different connections are possible, namely in the so-called meta (m) or para (p)-arrangement. Depending on the m- or p-aramid obtained, different material properties result, which we briefly outline below. If you would like to delve deeper into the chemistry of polymerisation and the different structures or the historical development of the materials, please refer to the Wikipedia page for "Aramid".
1.1.1 p-aramid
The best known p-aramid fibre is Kevlar (manufacturer DuPont), another well-known trade name is Twaron (manufacturer Teijin). The material is of course non-flammable, does not melt and has a decomposition temperature of 550° C. It is extremely high strength, which means that it is also used in ballistic bulletproof vests.
A disadvantage of the material, however, is its poor resistance to light. When exposed to direct sunlight, p-aramid loses its excellent tear resistance. Therefore it is always processed in a form that is UV-protected.
1.1.2 m-aramid
The chemical combination in meta position results in m-aramid which has the well-known trade name Nomex (DuPont) and Teijinconex (Teijin). With a thermal resistance of up to 370° C, m-aramid is mainly used for heat and flame protection products. However, it is 7 times weaker than the strength of p-aramid .
m-aramid also includes the fibre Kermel (manufacturer Kermel), a polyamide-imide with a slightly different but comparable chemical structure. The decomposition temperature of Kermel is 400° C. If you want to compare the chemical structures of the polymer chains, go to "Polyamidimide" on Wikipedia.
1.2 PBI
Fibres based on polybenzimidazole (PBI) have only been used in firefighting suits for about 30 years, compared to aramids, which date back to the 1960s. Developed for NASA's lunar program, the fibre demonstrates very good heat and tear resistance.
PBI with its golden colour became known in Germany primarily through the television images of the terrorist attacks in the USA in September 2011.
2. Natural fibres
Natural fibres needs be equipped with a flame-retardant finish for use by the fire brigade, identified by the abbreviation "FR".
2.1 Cotton FR
This is a natural fibre obtained from the seed fibre of the cotton plant. In contrast to synthetic fibres, the thermal decomposition temperature is lower, but the fabric is ideally suited for its main use in technical operations due to its very good wearing properties and pleasant skin-friendliness.
2.2 Viscose FR
Viscose is a cellulose fibre that, like cotton, can be made flame-retardant. Fabrics with a viscose content are characterised above all by their pleasant feel.
3. Fabric
The basic materials for the woven outer fabrics include the fibres presented here. Yarns are first made from these or from mixtures of these, which are then processed into a fabric as warp and weft threads with a specific textile weave.
m-aramid is mixed with a little p-aramid to increase the strength of the fabric.
This then results in the known fabrics:
Nomex Tough: 75% Nomex, 23% Kevlar, 2% antistatic fibre
Nomex III: 93% Nomex, 5% Kevlar, 2% antistatic fibre
Kermel HTA: 64.6% Kermel, 35.2% p-aramid, 0.2% antistatic fibre
Kermel HSK: 99% kernel, 1% antistatic fibre
PBI Matrix Gold: 40% PBI, 60% p-aramid
Nomex/viscose: 50% Nomex, 50% viscose FR
Kermel/Viscose: 50% Kermel, 50% viscose FR
the highly conductive antistatic fibres made of carbon or steel are also used to prevent the build-up of static on the garments through frictional electricity (cat-fur physics).
So which membranes are there and how do they differ?
The basic materials for the woven outer fabrics are the fibres presented here. Yarns are first made from these or from mixtures of these, which are then processed into a fabric as warp and weft threads with a specific textile weave.
m-aramid is mixed with a little p-aramid to increase the strength of the fabric.
This then results in the known fabrics:
Nomex Tough: 75% Nomex, 23% Kevlar, 2% antistatic fibre
Nomex III: 93% Nomex, 5% Kevlar, 2% antistatic fibre
Kermel HTA: 64.6% kernel, 35.2% p-aramid, 0.2% antistatic fibre
Kermel HSK: 99% kernel, 1% antistatic fibre
PBI Matrix Gold: 40% PBI, 60% p-aramid
Nomex/viscose: 50% Nomex, 50% viscose FR
Kermel/Viscose: 50% Kermel, 50% viscose FR
the highly conductive antistatic fibres made of carbon or steel are used to prevent the build-up of static on the garments through frictional electricity (cat-fur physics).
Which membranes are there and how do they differ?
The primary task of the membrane is to make the clothing waterproof against rain or fire-fighting water. This would work perfectly well, for example, with a simple polyethylene (PE) film inserted under the outer fabric, although it is of course possible to imagine that a "plastic bag" of this nature would completely block the outward transportation of sweat so necessary for thermoregulation. The membranes used today, on the other hand, achieve succeed in being a "barrier" to liquid water from the outside and at the same time "open" to water vapour from the inside.
This can be achieved with two different material concepts. The best-known solution is the use of the perfluorinated plastic PTFE. Owing to its microporous structure with pore diameters of approx. 0.2 µm, these are large enough to let water vapour through, but too small to allow water droplets to pass through from the outside. This microscopic "Swiss cheese" has an impressive pore density of over one billion pores per cm2.
A polyester or polyurethane membrane, on the other hand, is compact and non-porous, but consists of hydrophilic (water-friendly) and hydrophobic (water-repellent) areas at molecular level. Water vapour travels through the membrane along paths through the hydrophilic areas. The difference in concentration between the sides of the membrane drives the water vapour molecules outwards through the membrane.
The wafer-thin membranes described are usually bonded to a substrate as a laminate. For testing the quality, two different tests are carried out analogous to the mode of action "blocking or open"; these are explained in more detail in the answers to the following questions.
What are the requirements for reflective equipment and when does a high-vis vest exemption apply?
Firefighters on duty who may be subject to harm or danger by road traffic need to be protected using warning or cordoning-off measures in accordance with the provisions of the German accident prevention regulation (§ 17 Sec. 3 UVV "Fir Brigades" (GUV-V C53).
The implementation instructions for the regulation refer to BS EN ISO 20471 in general.
A suitable warning measure is the wearing of fire protection jackets
and trouser that meet the requirements of BS EN 469:2005, Annex B, BS EN 469: 2020, Section 6.2.6 (Visibility) and the HuPF. In contrast to BS EN 469, the HuPF prescribes the exact arrangement of the stripes.
These include the following requirements:
- Sufficient visibility during the day thanks to fluorescent material and at night through retroreflective material. The retro-reflective material (e.g. silver) is applied to the surface of the garment over a minimum area of 0.13 m² and must be visible from all sides. The minimum surface area of the fluorescent material (e.g. yellow) is 0.2 m². For a material with combined properties, the minimum area for jacket and trouser is 0.2m².
Design examples are shown in Annex 3 of the GUV. Of course, other arrangements or design suggestions are also possible as long as the required minimum area is given.
-
The retroreflective and fluorescent strips are arranged so that
the contours of the body (sleeves, torso and legs) are clearly visible.
If the firefighters' protective clothing meets both requirements, an additional
high-visibility vest is not necessary. If the mandatory areas for the two stripes cannot be applied to the jacket alone, then they can be combined them with the firefighter's trouser that are to be worn at all times.
Model with combination stripes Model with stripes with combined properties
How should fire brigade protective clothing be washed correctly?
In basic terms, it needs to be said that washing is always stressful for clothing. Therefore: wash as little as possible, but always as often as necessary.
The manufacturer's washing and care instructions are key for washing the garment. If possible, the clothing should not be washed in laundry facilities privately at home laundry, but in special laundries or washing machines made for this purpose by the fire brigade.
Protective clothing should be washed separately (possibly harmful substances!), and dark and light colours should also be separated. The machine should only be filled to 2/3 of the machine's recommended loading weight.
Choosing an optimal detergent is difficult given the bewildering variety of products available on the shelves. Detergents for delicates and coloureds without optical brighteners or bleaching agents are preferable; a detergent for black textiles can be used for dark blue outer fabrics. Without referring to specific suppliers here, reference can also be made to special detergents for firefighters' suits here. Fabric softeners should not be used.
In general, detergents with an alkalinity of pH 9-11 and a washing temperature of 60°C remove dirt and oil effectively and hence provide adequate cleaning action. A higher temperature and the use of more aggressive detergents can cause a visual change in the outer fabric due to discoloration. Before washing, the zips and Velcro fasteners need to be closed, the carabiners, braces and knee pads removed and the garment turned inside out. In the event of extremely heavy soiling, the garment can be sent for dry cleaning if the care instructions allow.
The garment needs to be rinsed sufficiently when washed in a washing machine. To avoid creases, clothing should be stretched out on a washing line before drying. To protect the fabric against colour changes, drying should not take place in direct sunlight.
Alternatively, a tumble dryer can be used, but the drying temperature should not exceed 60° C. Ironing is recommended to reactivate the FC finish; the dry or steam iron should be set to medium heat (2 points, i.e. up to 150° C). It goes without saying that reflective stripes should not be ironed over .
We have dedicated a separate question to the subject of impregnation.
Does washing it have an impact on the protective effect of the fire brigade protective clothing?
The fibres of the outer fabric (Nomex, Kermel, PBI) are permanently flame-resistant, i.e. flame retardancy and non-combustibility are permanent (or inherent) properties that cannot be washed out. Contamination with oil and grease can reduce its efficiency, however.
The negative consequences of doing the washing are well known from everyday life: Shrinkage, colour loss and discoloration. The effect of a temperature that has been set too high or incorrectly "in error" can then be seen. To avoid this problem, a 60° C washing temperature should be maintained. At this temperature, compliance with the maximum permitted shrinkage for all components (including the sleeve cuffs) has been checked in accordance with the standard after five washes.
The colour fastness or, more casually, the decolourisation and discolouration of the garment, on the other hand, is not tested according to BS EN 469. In contrast to the HuPF, the authenticity check is missing in the BS EN 469 requirements profile. Discoloration can be counteracted by sorting the laundry into the same colours. Bleaching is, as mentioned, a purely visual and aesthetic defect. The cause is generally due to the poor dyeing action of aramid fibres. Technically, discoloration does not alter the efficiency of the clothing.
Another negative influence of washing, secondly, is not immediately visible to the eye, but becomes apparent as soon as the first rain shower take place: the decrease in performance of the outer fabric's water-repellent finish. Since we don't want to leave you out in the rain, we have dedicated the next two questions to this topic (FC Finish).
What is FC equipment?
For a surface to be wettened by a liquid or for a liquid to roll off as a drop is a question of surface tension. In order to make the outer fabric water and dirt-repellent, it is also treated with fluorocarbon (FC) in a finishing step. Applying this chemical reduces the surface tension and makes the fabric hydrophobic. Paraffins, waxes, silicones or fluorocarbon are suitable as impregnating agents. In the area of protective clothing, fluorocarbon compounds are the measure of all things. An effective finish is weakened by washing, and will therefore deteriorate from wash to wash. Therefore, re-impregnate in line with the washing instructions. If possible using a spray so as not to impair the performance of the lining, membrane and insulation. In order to test the effectiveness after five washes in addition to the unwashed textile, BS EN 469 previously provided for the spray test according to BS ISO 4920. A textile sample is "sprinkled" with a nozzle at an incline of 45° and the wetting is assessed visually on a scale from 1 to 5. A good FC finish must achieve a rating of ≥ 4 after five washes at 60° C. However, it is also important for the finish to be thermally activated by the heat in the tumble dryer or with ironing. In the HuPF, the simple and practical spray test is still given, in the new BS EN 469, on the other hand, only a resistance test to penetration by the liquid chemicals sulfuric acid and xylene is required. This, together with the fact that the HuPF also includes a sprinkle test in the performance test, makes the difference in the requirements clear regarding "water from outside" between the current BS EN 469 and the HuPF.
How is fire brigade protective clothing correctly impregnated?
This is a difficult and controversial topic.
The efficiency of the FC finish is reduced by washing. Thermal reactivation with the help of tumble drying and/or ironing is therefore necessary after washing. The care instructions indicate after how many washes this should take place. You can check the extent to which the water repellency still works easily yourself by performing a simple test. To do this, place a few drops of water on the outer fabric and observe the continued reaction. If the drops remain and roll off easily, water repellency is good; if, on the other hand, the drops quickly soak into the fabric, the finish is lacking.
In order to change this, the post-impregnation agent needs to be added to the final rinse in the wash. A significant disadvantage of this process is that not only the outer fabric, but all layers of the garment become hydrophobic. The adverse effect on the behaviour of the lining was proven in a study by the Hohenstein Institute and published in "Brandschutz" (fire protection) (08/2015).
The absorption of moisture, which is required for transporting perspiration, is now reduced by the "co-hydrophobisation" of the lining, and the parameters descriptive of wearer comfort deteriorate permanently. For those interested, we recommend reading the discussion "Pros and cons of impregnation" by J. Thorns published in the same issue.
An alternative to treatment during rinsing could therefore be spray impregnation from the outside on one side of the fabric, as already mentioned above.
Special suitability tests for firefighter protective clothing
How is the water-tightness of the garment measured?
What is known as the water column is measured according to BS EN 20811 to determine water tightness from the outside. The membrane is exposed to steadily increasing water pressure on one side until the first three drops become visible. The water pressure required for this in mbar can be converted into the unit 'water column', 1 mbar roughly corresponds to 10 mm water column. The membrane of firefighter protective clothing must meet 200 mbar or 2 m water column according to BS EN 469.
The second suitability test for the membrane, namely its ability to let water vapour through, is described in the question that addresses the Ret value.
What is the Ret value?
A decisive contribution to thermoregulating the body to a constant core temperature of 37°C is the ability to secrete water, in other words to sweat. The high evaporation heat of the water make it possible to cool down the body during e. g. great physical exertion. The output of sweat can range between 2-4 l an hour. Thermoregulation is particularly important to the fire brigade, since excessive levels of physical exertion can also lead to further exposure to heat and radiation. Good transportation of sweat through the clothing can be essential for survival. Before the "worst case" of heat collapse sets in, an increased core temperature above 37° C leads to a significant increase in incorrect reactions caused by heat stress.
The good "breathability" of clothing can counter this potential risk.
How is the water vapour transmission resistance 'Ret' (Resistance Evaporation Transmission, unit m2 Pascal Watt-1) measured and why is it referred to as resistance? The measurement principle of the thermoregulation model for human skin according to BS EN 31092 (Skin model) consists of using a porous metal plate (model for the skin) to generate a flow of water vapour in a closed room, which is driven by a difference in the partial pressure of the water vapour (or, to put it casually, a difference in the concentration of water vapour in the room). From the high partial pressure area in the metal plate, water vapour migrates into the room with a constant humidity of 40 % RH. So that this current is only determined by the gradient in the partial pressure and not by the temperature differences as well, work has to be carried out at a very constant temperature or under isothermal conditions, in other words, the test room must be very well insulated thermally to 35° C.
If you cover the metal plate with a textile fabric, the flow of water vapor will decrease. In analogy to an electric current, the textile can be viewed as a resistor that slows the flow of particles. It turns out that in the textile structure of a firefighter's jacket, the membrane it contains hinders the flow of water vapour the most, the membrane being the "bottleneck", so to speak, for the rapid removal of sweat to the outside air. The individual Ret value of the membrane is thus greater than that of the outer fabric or the “light” lining.
BS EN 469 requires that the total resistance of the structure does not exceed 30 m2 Pascal Watt-1 for good wearing comfort. The lower the Ret value, the more conductive or breathable the clothing is for sweat and the better the wearing comfort of the protective clothing.
Today, however, there is a growing belief that the Ret value alone does not do justice to reality. In fact, the Ret value only describes the state of "vaporous sweating". For this reason, a second key figure records the transport of sweat during "liquid sweating". How quickly the sweat is absorbed by the textile structure and released again is characterised by the Kf value. This buffer effect of clothing is classified into three performance levels, the best performance level must achieve values of Kf > 0.7.
In contrast to BS EN 469, this part of the performance test is part of the HuPF.
What is the Thermoman test?
A firefighter with practical experience will wonder why testing the entire clothing under the "worst case scenario" of a "flashover" is only optional in BS EN 469. The most important test for use in internal operations can, but does not have to be, carried out for the certified suitability of a fire brigade suit. The background to this is the CEN (European Committee for Standardisation), which is responsible for European standardisation, with its principle that a test cannot and should not be passed when "injuries" occur, in this case up to 2nd degree burns. HuPF, Parts 1 and 4 sees this differently, here the Thermoman test or, as it is correctly called, "The flame test of a complete item of clothing using a sensor-equipped manikin" is mandatory. In line with BS ISO 13506, a life-sized metal test dummy equipped with 122 test sensors is dressed in overcoat and overtrouser. In a fire container, gas burners are distributed around the dummy, which simulate what is called a "flashover" with temperatures ranging from 800 - 1000° C after ignition for 8 sec. The measuring sensors distributed around the dummy record the rise in temperature for up to 1.5 minutes after the flames have gone out. Based on the registered heat flows, a special software application calculates the 2nd and 3rd degree burns to be expected over a specific body area. According to HuPF Part 1, only two sensor fields with 2nd degree burns and no field with 3rd degree burns may be present in the area covered by the overcoat.
The non-flammability of all clothing parts, including the zips and other accessories, is a basic requirement for good performance. Likewise, if the outer fabric does not break open after the flame is applied is evidence of a positive result.
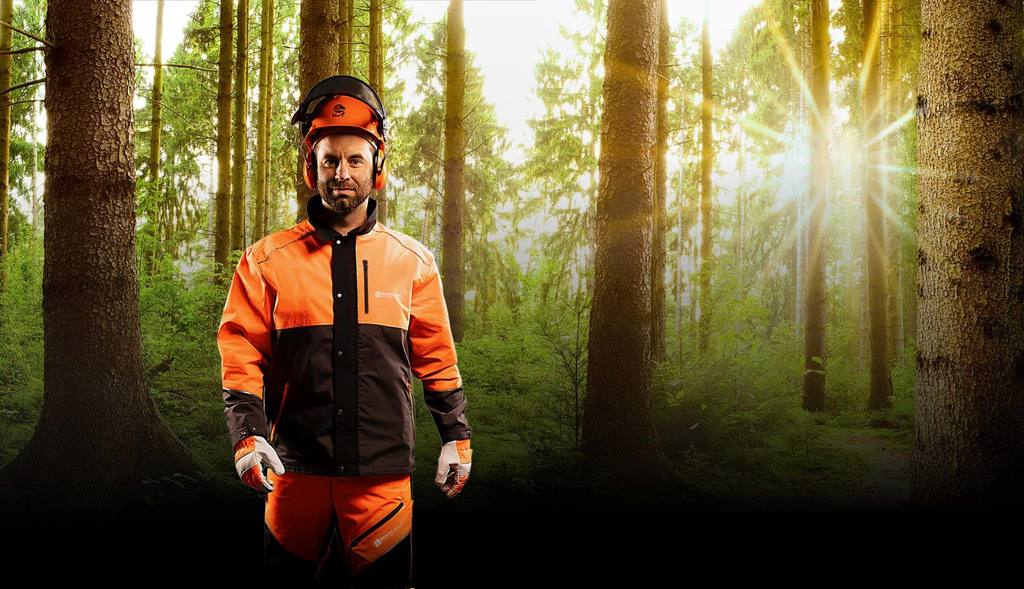)
Forest clothing
What is the currently valid standard for cut protection clothing?
The previous standard BS EN 381 has been revised intensively in recent years, and has now been published as the new worldwide standard BS EN ISO 11393 in six parts. Part 1 deals with the test stand itself, Part 2 with leg protection, Part 3 with footwear, Part 4 with protective gloves, Part 5 with protective gaiters and finally Part 6 with cut protection jackets.
Leg Protection
Three design specifications are described for the leg protection described in BS EN ISO 11393-2: Form A and C for trouser and Form B for chaps (leggings, the form is known from Westerns). While Form A essentially only covers the front of the leg, Form C offers all-round protection for the entire leg.
The actual cutting test lies at the centre of the test: structure, function and test parameters are described in Part 1. The cut protection test is not only carried out on medium size trouser, but also with the smallest and largest size in the size key offered. As a rule, the cut is only made after five washes, usually at 60° C. The cut protection classification is based on the chainsaw's running speed: Class 1 at 20 m/sec, Class 2 at 24 m/sec and Class 3 at 28 m/sec. The chainsaw, rotating at the selected speed, falls from a height of only 2 mm at an angle of 45 ° onto the trouser fixed in the test stand. The number of intact layers is decisive for the quality of the cut protection package; damage to the last layer "above the skin", i.e. the lining, is considered a cut and is considered a fail.
What is new is that in addition to the cut protection itself, the comfort of the trouser is also assessed. in this respect, the wearer should be able to lunge with kneeling leg without significant impairment in the gusset area (crotch area). Climbing unencumbered over a 60 cm diameter tube lying on the ground should also be possible without any problem.
Cut protection jacket
With jackets, the accident scenario is one where a work colleague gets injured while working in tandem on a lifting platform.
The standard requirement has been modified here so that the jacket receives a higher level of acceptance and is therefore also worn in the corresponding situations. The test steps on the arm are now also placed at a 45° angle.
In addition to the test speed listed for the leg protection, the jacket can also be tested according to Class 0 with a chainsaw speed of 16 m/sec.
Two jacket models are available: Form A protects the shoulder area and the top of the sleeves at the front, while Form B protects the entire front area, the shoulder and the top of the sleeves.
How does cut protection clothing work?
Cut protection clothing is designed to protect the wearer from serious injuries when an accident occurs with a motor-driven chainsaw. The various accident scenarios that are possible in practice means that we always have to be clear that one hundred percent protection can never be given. With the introduction of the chainsaw driver's licence and the accompanying obligation to wear protective clothing, it has been shown however that the number of accidents has decreased quite significantly. A chainsaw operator's license and personal protective measures (cut protection trouser, gloves, shoes and helmet) are a prerequisite for working with the chainsaw outside of your own property; a violation can lead to a fine of up to €500.
How do such chainsaw protection trouser work? A textile fabric is a flat structure that is created by linking a minimum of two threads, namely warp and weft threads. These meet at an angle of 90° and, depending on the textile construction, a distinction is made between the three basic types of plain, twill and satin weave. With plain weave, the weft thread is alternately placed over and under the warp thread. In sum, both thread systems are firmly connected to one another. with the cut protection insert, it is different; here the warp and weft threads lie unconnected on top of one another. To make sure this construction does not fall apart, the threads are held together by a very thin binding chain. The great advantage of this so-called Raschel fabric is that the threads can be pulled out of the construction very easily. If high-strength yarns based on polyester or polyethylene are used, these are torn out when the chainsaw hits the ground and then block the saw's drive wheel.
To provide effective protection, this has to take place in a fraction of a second.
How should cut protection clothing be correctly cared for and washed?
The clothing should be washed as gently as possible, since the mechanical stress can impair the effectiveness of the cut protection insert. The washing temperature should no more than 60° C using a standard detergent without a fabric softener. After washing, the clothing should be pulled into shape while wet and dried on a washing line, but not in direct sunlight if possible. Do not use a tumble dryer. The clothing can be re-impregnated.
You should always remember to treat your clothing with care and attention. A well-functioning cut protection system will return the favour if an accident occurs!
It goes without saying that any damage to the trouser should not be repaired with a needle and thread, rather the trouser should be replaced immediately. As always, the following also applies here: SAFTY FIRST!
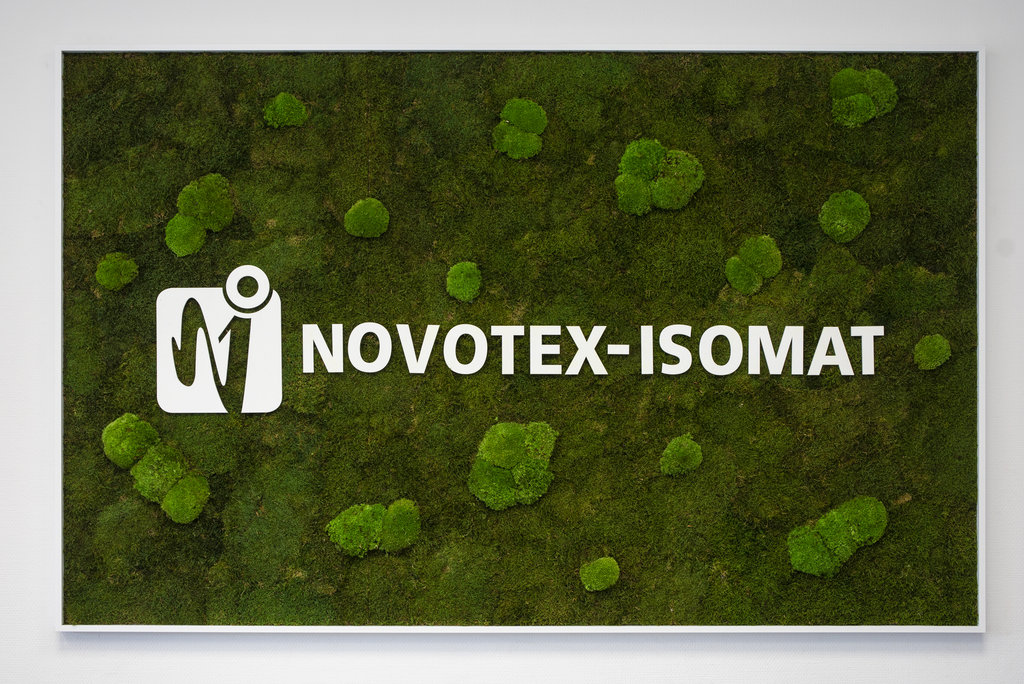)
General
Where can I buy Novotex safety clothing and accessories?
In principle, Novotex-Isomat products can be purchased from the Novotex reseller of your choice or in your area. We will be happy to help you find a suitable reseller close to you. To do so, simply follow our instructions regarding: “How can I contact the Novotex team?”
How can I contact the Novotex team?
The Novotex team will be happy to answer any questions you may have from Mondays to Fridays. You can contact us by phone, post or email. You can find all the information you need under the heading Contact Person or Contact. Beyond this, however, you can also contact the Novotex reseller of your choice. They already have a great deal of information about our product portfolio and can advise you well.
Where can I find certificates and other documents to download?
In addition to the individual products, you will find the corresponding information on our website, which displays and provides the standards, measurement tables, declarations of conformity and other information. The Novotex team will be happy to answer any further questions you may have. To do so, simply follow our instructions regarding: “How can I contact the Novotex team?”
How can I find out about news, interesting information and new products?
You can of course contact the Novotex reseller of your choice for up-to-date information and the latest Novotex-Isomat products. You can also read all the Novotex news on our website under the highlights section on the launch page or follow us on LinkedIn or Instagram. #novotexisomat